介绍完这些后,本次活动正式开始。首先,主办方带领车主们参观了冲压车间,在这里,一块块钢板瞬间变成汽车的骨架,目前临港工厂有两条冲压线,未来还会建成第三条,均是全自动化生产,减少了人员的参与,既保证了安全,又提高了工作效率。
对于冲压后的骨架也有专业的技术人员进行逐个检验,主办方告诉大家,下一道焊接工序是自动化的,因此对于冲压件的质量要求也非常高,专业的成品检查非常严格,这也意味着上海汽车在进行每一步工序的时候都必须经由100%的严谨把关。
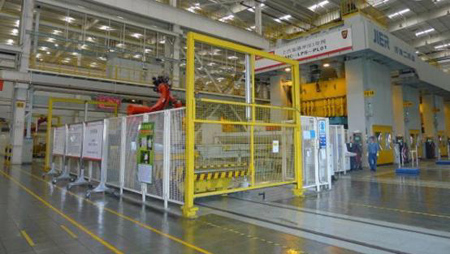
在临港工厂已经基本实现了自动化焊接,最高的焊接自动化率可以达到99%。而且实现了充分柔性化生产。与传统的平台相比,临港工厂焊接支架是打开的,这里叫Open
gate + butterfly,不同的车型可以自动的更换工位,可以实现3个平台6种车型共线生产。
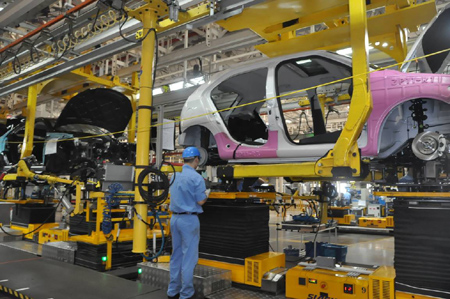
焊接好的车身直接从一条传送带,运送到油漆车间。荣威和MG均采用了水溶性电泳、无铬钝化,水性漆设计,而且所有的废弃物都会被焚烧。由于油漆车间有洁净度的要求,只要有大于10微米的灰尘,喷好漆以后就是一个缺陷产品。为了保证喷漆质量,这里不允许参观,车主们也只能绕过喷漆车间,来到总装车间。
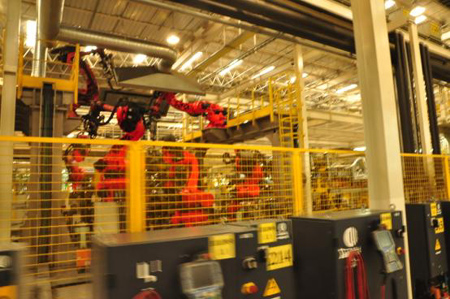
在总装车间,车主们大呼神奇,亲眼见证车壳子一步步变成一辆车。在这里有三个值得我们关注的问题。一是自动质量控制点,所有的东西,比如说扭矩,都通过计算机控制,而且记录下来,一旦螺丝拧紧过程中出现问题,就可以从计算机中查到,从而保证每个螺丝的装备质量。另外,在总装车间可以看到一排排自动行驶的小车,这就是SPS系统(就是随行料架)。一个工厂要生产4、5款车型,每个车型配置都不一样,如何实现在一条总装线上生产这么多的车型呢?就是靠这个SPS系统。SPS系统完全由电脑控制,料架和车子一起走,一个车子的物料配好放在车子上,料装完这个车子就装完了。第三个就是安灯系统,如果生产线上的装配工人发现问题,就拉动拉绳,流水线就会停下来,直到问题解决。精益化、敏捷化、柔性化、模块化生产方式贯穿了整个生产流程。